Motor control systems are widely used in rail, industrial automation, etc. With the development trend of AC control, digitization and integration of motor control systems, the use of semi-physical simulation to improve the development efficiency of the system has received more and more attention. In the test verification stage for the finished servo controller, the HIL hardware-in-the-loop simulation can be divided into signal level, power level and mechanical level according to different test objects and test methods.
Introduction to semi-physical simulation of motor control system
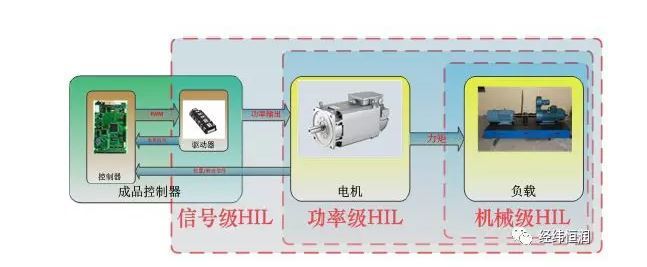
Signal Level HIL: The test system utilizes FPGA-based high-speed real-time simulation techniques to simulate inverters, motors, and mechanical loads. The test object is a servo controller. The signal level HIL has been widely used in various industries in China, and has the characteristics of low cost and flexible construction. However, since the controller is often integrated with the driver and the driver, the signal level HIL must be supplied by the controller to be tested. Otherwise, the current loop cannot be completed. At the same time, the signal level HIL cannot be realized to the inverter (driver). Amplify part of the circuit), so the test object has a narrow coverage, and the signal level HIL can be selected when testing the motor controller control logic separately.
Mechanical grade HIL: Using the simulation equipment to mechanically connect with the motor and controller to be tested through the motor drive table shelf system to simulate the mechanical load. The test object is a complete servo control system including controller, driver, motor, and transmission. This method is the most complete test method for the servo system, and is often used as a means of factory inspection, but it also has limitations such as high cost, long cycle, large footprint, and it is difficult to simulate multi-degree of freedom load. A mechanical grade HIL can be used when testing the response characteristics of the complete motor drive system to the load.
Power Stage HIL: The test system utilizes FPGA high-speed real-time simulation technology, inverter-to-drag technology to simulate motor and mechanical loads. Test objects are controllers and drives. This method can achieve more comprehensive testing for the control system, but due to its high technical difficulty, it has long been monopolized by foreign manufacturers, and the price remains high. The power stage HIL does not require the current feedback interface of the controller to be tested. The motor load can be changed by adjusting the parameters. The power level HIL can be selected when testing the motor controller logic and the performance of the driver under real current conditions.
â— Advantages of power level HIL:
â—† Control algorithm driver for test controller finished product without interface modification of controller finished product
â—†Test the performance of all sensors of the finished controller in high frequency and high current environment
â—† One power level HIL platform can cover the test of various motor controllers, and can simulate different motors and loads by modifying the model parameters.
â—† There is no safety hazard of mechanical HIL, and it can simulate multi-degree of freedom load
â—† There is no coaxiality problem in mechanical grade HIL
â—†Small footprint and short implementation period
â—† can achieve fault injection
Runke Universal Power Stage HIL: PowerHIL
â—Basic principles and composition
PowerHIL is mainly composed of HiGale real-time simulation subsystem and motor power simulation subsystem. The HiGale real-time simulation subsystem is responsible for the real-time solution of the motor model and the current composite control model; the motor power simulation load subsystem simulates the three-phase load current through the converter technology. The principle of motor power level HIL is as follows:
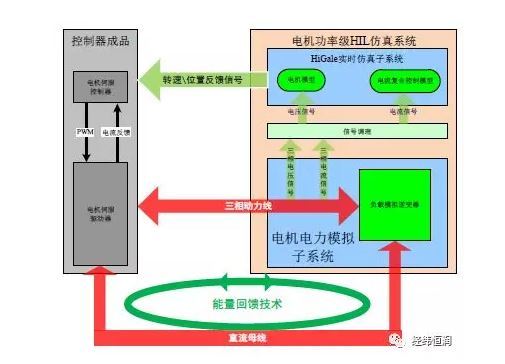
The motor power simulation subsystem includes an innovative main circuit, a drag reactor, a signal acquisition unit, a current sensor, and a voltage sensor. High-bandwidth, high-precision three-phase current control is realized by pulse distribution technology, multi-bridge parallel technology, and composite control technology to achieve high dynamic simulation of electrical characteristics of the motor.
In addition to the HiGale real-time simulation subsystem and the motor power simulation subsystem, PowerHIL includes a signal adaptation unit and a wire break test unit. The signal adaptation unit is used for the cable management, docking controller finished interface; the wire break test unit is used for real-time simulation machine output signal measurement and disconnection test. The layout of the cabinet is as follows:
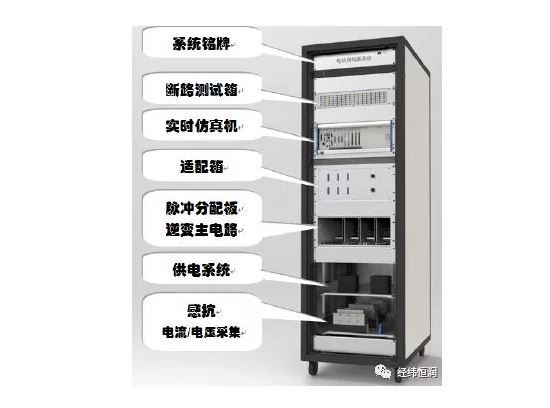
The following figure shows the effect diagram and experimental monitoring interface of a power-level HIL of a small power controller in China. In the effect diagram, the black curve represents the motor speed, and the red, green and blue curves represent the U, V, and W phase currents, respectively.
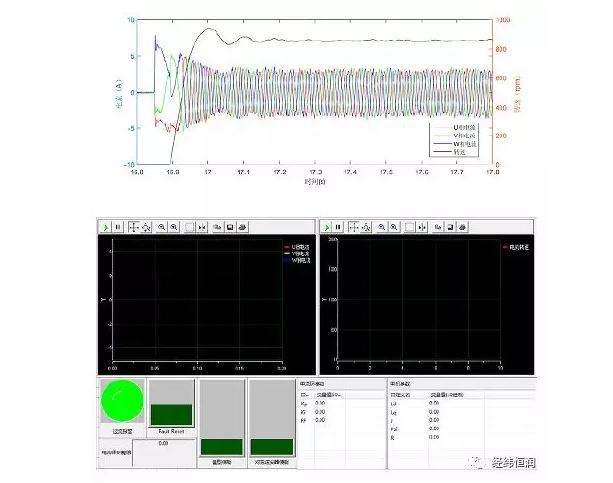
â—Main features:
â—† High-speed dynamic simulation of 100ns-class motor inverter based on FPGA
â—† Can achieve the overall test of the motor controller finished product for the controller driver
â—† High dynamic test controller control algorithm and all sensor performance
â—† Can verify the performance of the drive in real current environment
â—† No need to develop additional signal level current feedback interface
â—† Innovative main circuit pulse distribution technology, based on FGPA motor simulation board, the single-phase PWM frequency of the tow inverter can reach 20KHz
â—† Self-contained energy feedback technology, low power supply bus current, low energy consumption
â—† Customized experiment monitoring interface
â—† Can achieve a variety of fault injection
â—† Multiple protection logic to prevent equipment damage
â— Customer income:
â—†You can test all the controllers of the controller's finished controller without any interface modification, and quickly expose the product problems. Improve the efficiency. Only by adjusting the parameters, the motor parameters and load torque can be changed.
â—†With rotary transformer, photoelectric encoder and Hall signal simulation, the same platform can simulate multiple types and multiple parameters of the motor, so that the same platform can complete the test tasks of various controller products with rich fault injection function. Test the fault protection function of the finished controller
â—†Small footprint, no mechanical safety hazards
White Tissue Paper Bulk,Custom Tissue Paper,Bulk Tissue Paper,Bulk Of Tissue Paper
DONGGUAN YEE HUP TRADING CO,.LTD , https://www.dgyeehupack.com